В началото на XXI век японският автомобилен производител Toyota задминава по пазарен дял дори гиганти като General Motors и Ford и се превръща в най-големият и печеливш автомобилен производител в света.
Този успех е възможен благодарение на уникалната система за производство, която десетилетия наред се изгражда и усъвършенства в Toyota.
Тази система е известна като “Производствена система на Toyota”. Тя става толкова популярна, че се изучава и прилага от огромен брой други компании от всякакви браншове и държави. Нека я разгледаме.
Производствена система на Toyota
Производствената система на Toyota, или казано накратко TPS (от “Toyota Production System”) е завършена система, разработена от Toyota, която включва както нейната философия, така и практиките й за управление.
Производствената система на Toyota организира производството, включително взаимодействието с доставчици, клиенти и персонал. Главната й цел е да премахне т.нар. “муда, мура и мури” от всички нива в организацията.
По-конкретно, чрез TPS се цели премахване на прекалено голямото натоварване на хора и машини (мури), несъответствията в нормалния темп на бизнес операциите, които водят до флуктуации в обема на производството (мура), както и елиминиране на загубите – всяка дейност, която консумира ресурси, но не създава стойност (муда).
Производствената система на Toyota е разработвана и усъвършенствана десетилетия наред, най-вече в периода 1948-1975 г., благодарение на усилията на няколко поколения висши мениджъри от семейство Тойода и водещи японски индустриални инженери.
За да се разбере по-добре замисълът на TPS, заслужава си да се направи кратък исторически преглед на развитието на самата компания Toyota през годините.
Историческо развитие на Toyota и TPS
Формално, Toyota Motor Company e основана през 1937 г. Тя обаче не възниква от нищото.
Идеята за производство на автомобили се заражда много по-рано и принадлежи на Сакиши Тoйода, роден през 1867 г.
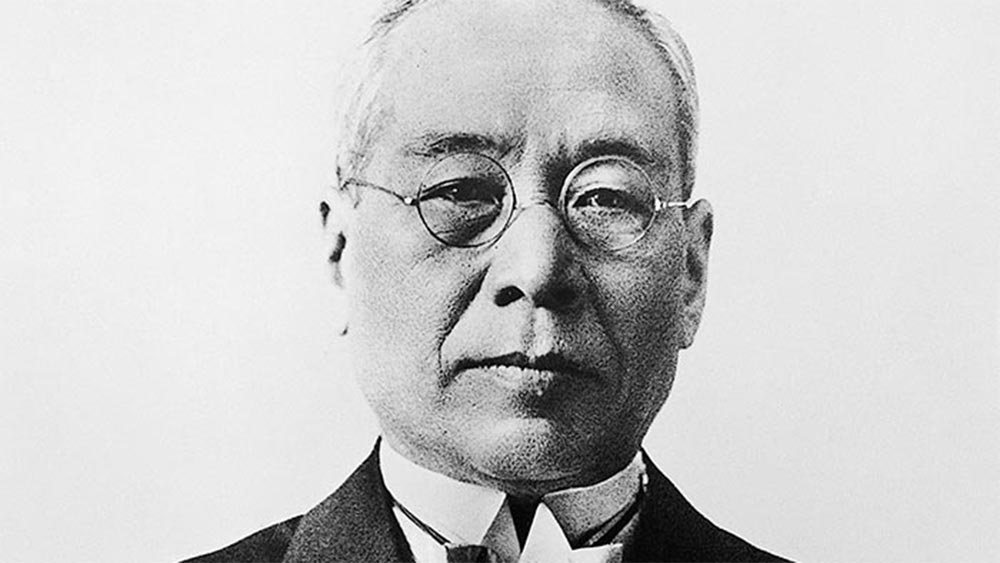
Като първороден син, традицията прави Сакиши Тoйода глава на семейството и наследник на своя баща и на неговата професия – кофражист.
Сакиши Тойода обаче не проявява интерес към професията на баща си и от 1885 г., в продължение на 35 години, се занимава с усъвършенстването на тъкачни станове.
През 1910 г. Сакиши Тойода основава собствена фирма за производство на тъкачни станове – Toyoda Spinning and Weaving Company. През 1924 г., с помощта на своя син Кииширо, той създава напълно автоматизиран тъкачен стан, а през 1926 г. и новата си компания – Toyoda Automatic Loom Works.
Без да има образование, Сакиши се самообучава по метода на проби и грешки. Той вярва силно в способността си да получи необходимите знания, работейки непосредствено с промишлено оборудване. Отличителното за него е, че осъзнава важността от непрекъснато усъвършенстване на оборудването, независимо от състоянието на конкурентите.
Сакиши Тойода е убеден, че нито един технологичен процес не е достигнал такава степен на развитие, от която да е невъзможно по-нататъшно усъвършенстване. Политиката на непрекъснатите усъвършенствания става част от неговата промишлена философия.
През 1929 г. Сакиши Тойода продава патентните права на своя автоматичен тъкачен стан на една английска фирма за сумата от 100 000 британски лири. И тъй като е убеден, че в бъдеще автомобилите ще станат перспективна стока, предлага парите на своя син Кииширо Тойода, но при условие той да ги инвестира в изследователска работа за създаване на автомобили.
През 1930 г. Кииширо Тойода приема условията на своя баща, поема управлението на компанията и се захваща с изследване и разработване на автомобили.
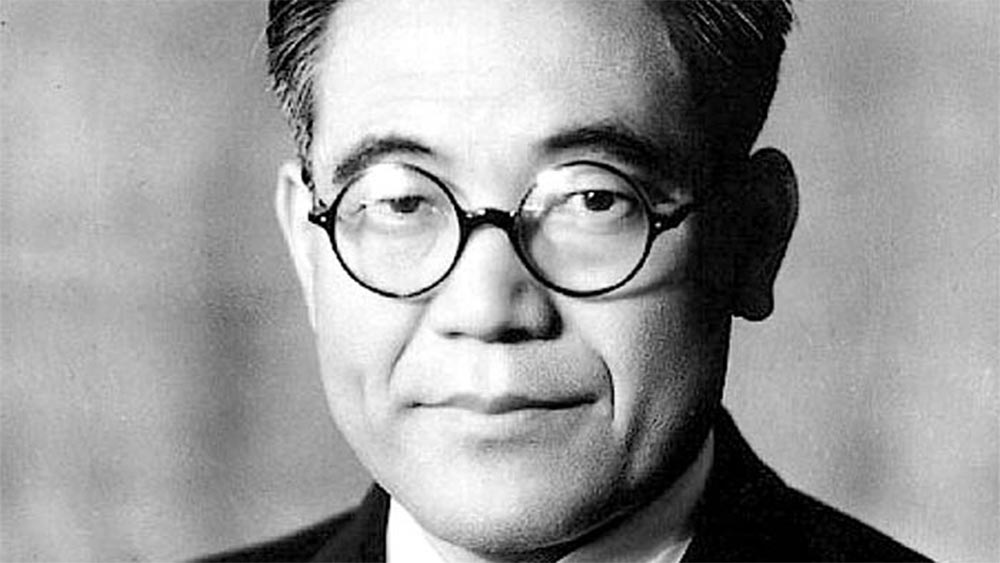
Кииширо Тойода е роден през 1894 г. и е най-големият син на Сакиши Тойода. Дипломира се през 1920 г. в Токийския университет като инженер по машиностроене и още в същата година постъпва в компанията на баща си Toyoda Spinning and Weaving Company.
През 1930 г., след смърта на баща си, Кииширо Тойода поема управлението на компанията и съгласно волята на баща си, пристъпва към производството на автомобили.
Като начало, Кииширо Тойода отделя едно помещение в Toyoda Automatic Loom Works, в което започва самостоятелно да изучава неголям двигател с вътрешно горене. През 1934 г. той и негови сътрудници завършват разработката на първия собствен двигател от модел А. Първият лек автомобил и първият товарен автомобил с този двигател са сглобени през месец май и август на следващата 1935г .
Тъй като разходите за издръжка на автомобилния отдел са бреме за компанията Toyoda Automatic Loom Works, Кииширо стига до извода, че единственият начин да се завоюва пазар е да създаде самостоятелно предприятие.
През 1937 г., след одобряване на тази идея от съвета на директорите на Toyoda Automatic Loom Works, получаване на необходимия кредит и пускане на акции, официално се учредява компанията Toyota Motor Company. В началото Кииширо Тойода е неин изпълнителен вицепрезидент, а от 1941 г. става и президент на компанията.
След края на Втората световна война Toyota Motor Company се оказва в тежко положение, тъй като всички работници се включват в стачка, протестирайки против решението за масови уволнения. След неуспешен опит да потуши конфликта с работниците, Кииширо Тойода подава оставка като президент на компанията. След това, готвейки се да оглави отново компанията и да стартира производството на автомобили, Кииширо Тойода умира внезапно от мозъчен инсулт.
И така, Кииширо Тойода е наследник на Сакиши Тойода и формален основател на Toyota Motor Company. Но неговият принос е далеч по-голям от самото основаване на компанията.
Кииширо Тойода осъзнава, че за да се конкурира успешно с такива могъщи компании като General Motors и Ford, Toyota трябва да влага средства за развойно-внедрителска дейност. Именно поради това, през 1936 г. Кииширо Тойода организира изследователска лаборатория на Toyota Motor Company в Токио.
Кииширо Тойода иска да разработи изцяло японска производствена система, която да отчита характерните за Япония ограничения от пространство и ресурси. Той мечтае да създаде система, в която, за разлика от GM и Ford, нито един елемент да не се създава преди да възникне необходимост от него. Това, според Кииширо Тойода, е разковничето да се избегне съхранението на огромни количества детайли, които съответно водят и до значителни разходи на средства.
Така, основен лозунг в Toyota става “Точно навреме” (Just in time). В съотвествие с философията “Точно навреме”, нито един детайл за автомобил не трябва да се създава преди да се появи необходимост от него.
Идеята на Кииширо Тойода за “Точно навреме” заляга като основополагащ елемент от производствената философия на Тойота. В пълна степен възможностите на “Just in time” се развиват и използват след 50-те години на XX век при следващите висши ръководители на Тoyota.
А следващият значим ръководител на Toyota е Ейджи Тойода.
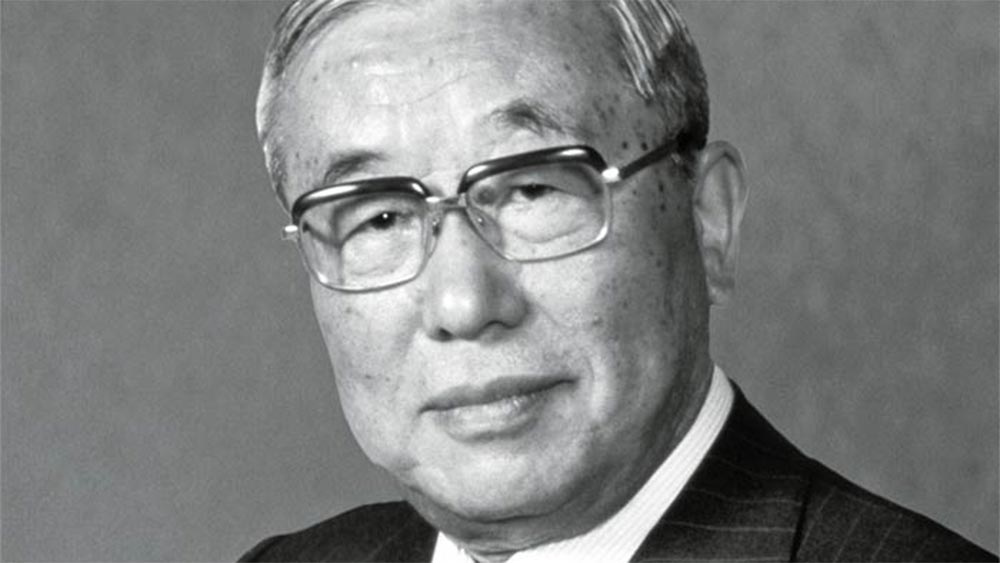
Ейджи Тойода е роден през 1913 г. Той е първи братовчед на Кииширо Тойода, тъй като неговият баща е брат на Сакиши Тойода. Ейджи израства в дома на Кииширо Тойода и е пълнокръвен член на семейството.
Ейджи Тойода завършва Машиностроителния факултет на Токийския университет през 1936 г. и постъпва на работа в Toyoda Automatic Loom Works, по-специално в лабораторията за проектиране на автомобили.
През 1947 г. в САЩ умира Хенри Форд – основател на Ford Motor Company, и фирмата се ръководи от неговия внук Хенри Форд II. Това отваря вратата за преговори между Ford и Toyota за създаване на съвместно предприятие.
Преговорите стартират през 1950 г. Благодарение на тях, японските инженери получават възможност да стажуват в американските заводи на Ford – пионер в серийното производство. Ейджи Тойода е първият служител на Toyota, който стажува в заводите в САЩ.
В Америка Ейджи Тойода научава много нови неща. Например, той с изненада установява, че техниките за серийно производство на автомобили не са се променили много в сравнение с 20-те и 30-те години на XX век.
Системата за серийно производство на Ford тогава е предназначена да произвежда ограничен брой модели автомобили, но затова пък в огромни количества. За да бъде в състояние да ги произвежда, компанията Ford притежава всичко необходимо – собствени рудници за желязо и каменовъглени мини, металургични заводи, система за снабдяване, големи пазари (вътрешен и международен), огромни налични парични ресурси.
От една страна, масовото производство и стандартизацията във Ford създават благоприятни условия за поевтиняване на автомобилите, а от друга страна позволяват внедряване на техническия прогрес.
Проучвайки производствената система на Ford обаче, Ейджи Тойода и други специалисти на Toyota установяват в нея сериозни недостатъци. Ето по-важните от тях:
- Свръхпроизводство в отделни сектори на производствената система, следствие от целта да се произвеждат огромни количества продукция;
- Складиране на големи стокови запаси в някои сектори и транспортирането им към други сектори, където тяхната обработка трябва да продължи.
- Неравномерен производствен поток с прекъсвания между отделните му етапи, което поражда финансови загуби;
- Невъзможност да се откриват дефекти в големите партиди продукция, което също води до загуби.
Toyota не може да си позволи икономии от подобно мащабно производство, защото не притежава такива ресурси, каквито има Ford. Затова, стратегията на японската компания, за разлика от тази на Ford, е да произвежда малки количества от различни модели, като използва една и съща монтажна линия, ограничени ресурси и капитал.
За да може да осъществи своята стратегия, Toyota взема решение да подобри производствената си система. Тя трябва да е такава, че да позволява гъвкаво производство на автомобили с високо качество, при ниски производствени разходи и кратки срокове за производство.
През 1951 г. Ейджи Тойода разработва петгодишен план за модернизация на Toyota, който включва обновяване на оборудването и усъвършенстване на производствените методи. Той осъзнава, че компанията е длъжна да работи по различен начин от западните фирми.
За провеждането на нужните промени, Ейджи Тойода кани в компанията Таичи Оно – един безспорен експерт.
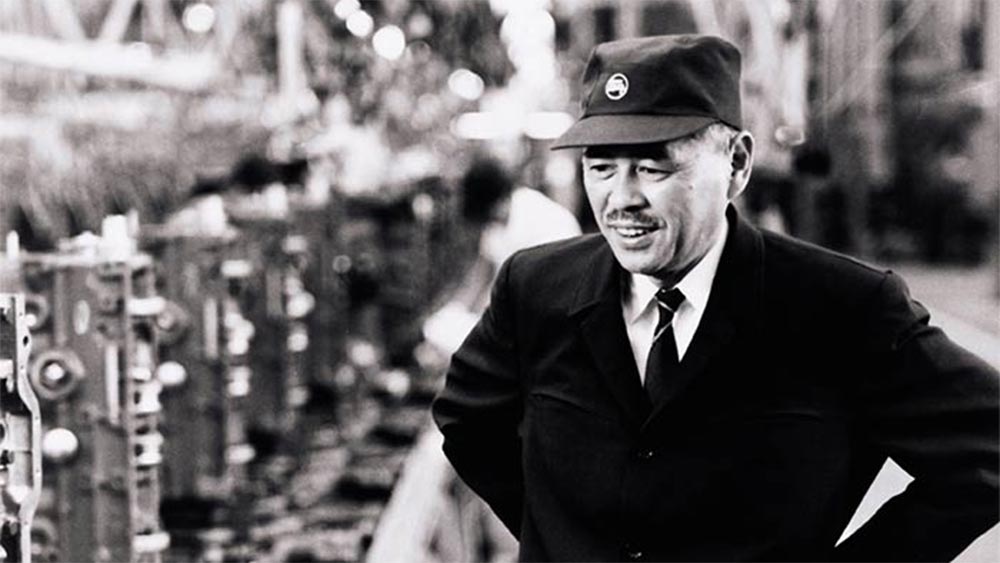
Преди да приеме поканата на Ейджи Тойода, Таичи Оно работи в продължение на 10 години като инженер по текстилно оборудване в компанията Toyoda Spinning and Wearing Company.
Поради тази причина, Оно е отлично запознат с производствената философия на компанията и с вижданията на самия Ейджи Тойода, който го подкрепя напълно в усилията му да модернизира производството на Toyota чрез създаване на цялостна производствена система.
Оно използва две основни идеи на Кииширо Тойода – за синхронизацията на преместваните възли при монтаж на изделията и за автоматизацията на контрола. Според Оно, машините трябва да се снабдят с контролни прибори за осигуряване на съответните технически изисквания на всички производствени детайли. Ако такъв прибор констатира отклонение от стандарта, той подава специален сигнал на оператора, който спира поточната линия до отстраняването на проблема.
Една от основните трудности, с която се сблъсква Таичи Оно, е как да се надмине икономията от мащаба на производството във Ford и едновременно с това да се постигне по-висока производствена гъвкавост. Това е наложително, за да няма струпване на огромни материални запаси и по този начин монтажните линии да работят непрекъснато.
Как постъпва Таичи Оно? Той съкращава рязко времето за пренастройка на струговете и монтажните линии, което позволява непрекъснато да се произвеждат неголеми партиди от различни модели автомобили.
В същото време, Оно създава специални програми в помощ за разрешаване на производствените проблеми. Така се раждат например наръчниците за “Общо профилактично обслужване на оборудването”, “Тотално управление на качеството”, “Непрекъснато усъвършенстване”, “Автоматизация” и “Доставки точно навреме на комплектоващи детайли”.
Всичко това са истински иновационни решения, които позволяват усъвършенстване на системата за масово производство на Ford и повишаване на нейната ефективност и гъвкавост. Ето защо с основание се счита, че именно Таичи Оно е създател на производствената система на Toyota.
Като високопоставен мениджър, Ейджи Тойота оказва пълна управленска подкрепа на усилията на Таичи Оно. Благодарение на това сътрудничество, само за две години Toyota постигa радикални подобрения в работата си.
През 1963 г., производствената система на Toyota се внедрява официално във всички подразделения на компанията. От този момент Toyota започва да изисква от своите доставчици също да използват тази система.
Резултатът е зашеметяващ. Toyota започва да предлага на пазара качествени автомобили на много конкурентоспособни цени.
През 1967 г. Ейджи Тойода става президент, а през 1982 г. и председател на съвета на директорите на Toyota. В същата година започва преговори с General Motors за създаване на огромно съвместно предприятие – компанията New United Motor Manufacturing Incorporated. То трябва да произвежда автомобили на основата на японския модел Corolla в закрития преди това завод на GM в Калифорния.
Проектът между двете компании е успешно реализиран. Това доказва, че прилагането на производствената система на Toyota е напълно възможно извън Япония, на Запад.
Следващият висш ръководител с голям принос за развитието на производствената система на Toyota е Соиширо Тойода.
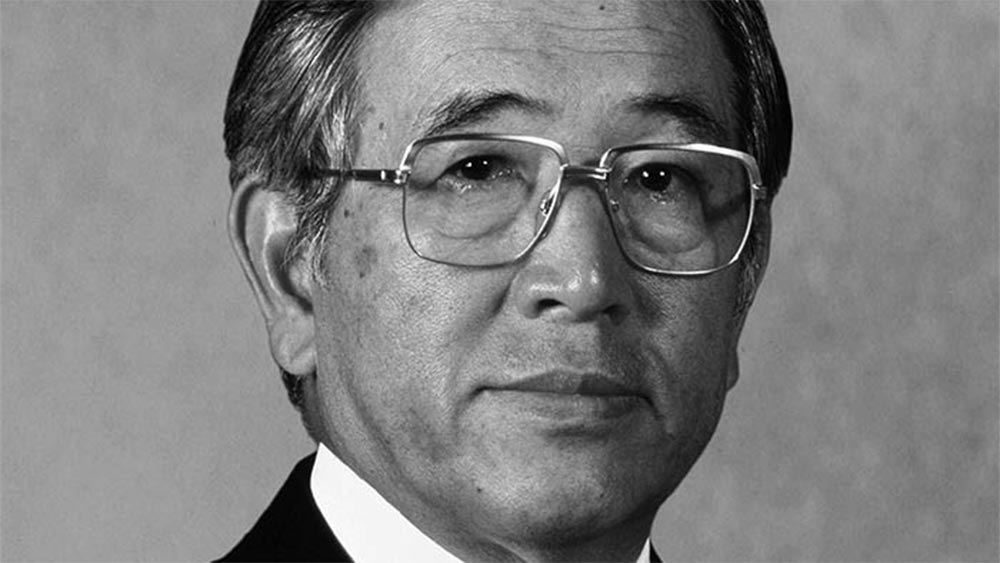
Соиширо Тойода е най-големият син на Кииширо Тойода. Роден е през 1925 г. Завършва Нагойския университет с диплома за инженер по машиностроене, а по-късно и получава научна степен „доктор по машиностроене”.
През 1952 г. Соиширо Тойода започва работа в Toyota Motor Company. По това време, компанията Toyota вече има своята нова производствена система и тя носи .
Оглавявайки отдел “Планиране”, Соиширо Тойода стига до извода, че компанията използва на много късен етап “кайзен” – философията на непрекъснато усъвършенстване. Практиката на отстраняване на дефекти по автомобилите, след като те са вече на пазара, подронва репутацията на Toyota.
В търсене на начини за повишаване качеството на продукцията, Соиширо Тойода внимателно изучава идеите на Уилям Деминг за управление на качеството.
По това време Деминг вече има голяма популярност в Япония. През 50-те години на XX век той изнася пред водещи японски бизнесмени цикъл от лекции по управление на качеството. В Япония е публикувана първата книга на Деминг и отново там той получава пълна професионална реализация, благодарение на което е познат днес като създател на концепцията за тотално управление на качеството.
Соиширо Тойода залага на идеите на Деминг за управление на качеството. Той изучава и внедрява в Toyota някои от тях. Счита, че за да бъде подобрена работата на производствената система на Toyota, е необходимо да се променят два аспекта от процеса на управление на качеството:
- Необходимо е процесът на управление на качеството да се систематизира по-добре.
- Необходимо е процесът на управление на качеството да се внедри във всяко подразделение на компанията.
Соиширо Тойода успява да реализира цялостна програма за управление на качеството във всички звена на компанията и през 1965 г. производствената система на Toyota е удостена с “Награда Деминг” – най-престижната награда по управление на качеството в Япония.
През 1982 г. Соиширо Тойода става президент на новосъздадената Toyota Motor Corporation, а след това и председател на съвета на директорите. Под негово ръководство Toyota се превръща в прочута международна корпорация.
📧 Безплатен бюлетин
Присъедини се към 2100+ души и получавай бюлетина ни, пълен с важни идеи и прозрения за професионално и личностно развитие.Принципи на TPS
През 1992 г. Toyota Motor Corporation публикува официална брошура с описание на своята производствена система.
В предговора на брошурата можем да прочетем следните думи:
“TPS е рамка за опазване на ресурсите чрез елиминиране на отпадъците. Хората, които участват в системата, се научават да идентифицират разходите за материали, усилия и време, които не генерират стойност за клиентите, след което тези разходи се избягват. Тази брошура не е ръководство. По-скоро, тя е преглед на концепциите, които стоят в основата на нашата производствена система. Брошурата е напомняне, че трайните подобрения в производителността и качеството са възможни винаги и навсякъде, където ръководство и служители са обединени в ангажимента си за положителна промяна.”
Кои са основните концепции в производствената система на Toyota?
Това са най-вече две концепции:
- Концепция “Точно навреме” (Just in time) – произвежда се само това, което е необходимо, само когато е необходимо и само в необходимото количество.
- Концепция “Джидока” (Jidoka) – автономизация, т.е. внасяне на човешки интелект в машините, способни самостоятелно да откриват първия дефект, веднага да спират и да сигнализират, че е възникнал проблем.
За да има гъвкаво производство на автомобили с високо качество, при ниски производствени разходи и кратки срокове за изпълнение, Toyota първоначално се обляга на идеята на Ford за “непрекъснат поток” или скъсяване на времето за използване на суровините до изработка на крайните изделия, което намалява сроковете за производство.
Японците доразвиват тази идея, като вярват, че “потокът” осигурява намаляване на запасите, изважда на показ проблеми и показва неефективните дейности, които изискват незабавни решения.
Всеки служител в Toyota е мотивиран да разрешава проблеми с неефективните действия, защото в противен случай производственият процес е обречен да спре. Например, в компанията всеки се старае да премахва осемте вида загуби (муда), дефинирани от Таичи Оно и допълнени от Шигео Шинго: свръхрпроизводство, изчакване, ненужен транспорт, прекомерна обработка, излишни запаси, ненужни движения, дефекти, неизползвана креативност (инициативи, творчество) на работниците.
Отчитайки, че свръхпроизводството на отделни етапи в производствения процес представлява голяма загуба за компанията, мениджърите в Toyota въвеждат т.нар. “изтегляща се система”, която взаимстват като идея от американските супермаркети.
Приложена към производството, изтеглящата система означава, че в производствения процес етап 1 не трябва да произвежда своите части, докато следващия етап 2 не изразходва своите наличности до границите на едно малко количество гаранционен запас.
Когато етап 2 достигне до гаранционния запас, той трябва да сигнализира на етап 1 да достави още части. Същата логика се използва и на следващите етапи, докато се стигне до крайния клиент.
По този начин изтеглящата система създава нуждата от подхода, известен като “Точно навреме” (just in time). С него става възможно да се реагира на всекидневните колебания в потребителското търсене.
Използвайки този подход, всеки работник (“етап”) в Toyota се третира като “клиент” и на него му се доставя точно това, което му е необходимо, при това точно навреме. Или, предходният работник (етап) винаги извършва това, което нарежда следващият.
В условията на производствена система с едноелементен поток, в Toyota много прецизно се открояват два въпроса:
- Какво е това, което иска вътрешният клиент на всеки следващ етап в производствената линия ?
- Какво е това, което иска крайният, външният клиент?
Така, през очите на клиента в Toyota могат да наблюдават всеки отделен производствен или бизнес процес, както заедно, така и поотделно. Благодарение на това могат да се разграничават операциите, които не носят добавена стойност от тези, които носят добавена стойност.
Операциите, които не носят стойност са загуби за компанията и за тях се вземат решения как да бъдат сведени до минимум или как да бъдат напълно отстранени. В Toyota се следи внимателно времето, което се изразходва за операции без добавена стойност, като стремежът е това време да се намали до възможния минимум.
Мениджърите на Toyota винаги проявяват невероятно постоянство в прилагане на инструментите, методите на производство и управленските системи, присъщи на производствената система на Toyota.
Някои от тях, които добиват широка популярност в света на управлението, са:
- Точно навреме;
- Джидока;
- Едноелементен поток;
- Изтеглящата се система;
- Кайзен;
- Муда, мура и мури;
- Хейджунка;
- 5 Защо;
- 5S;
- Работа в екип;
- Генчи генбуцу.
Неспирният успех на Toyota при внедряването на различни управленски практики се корени в бизнес философията на компанията и в следването на ясни принципи.
14 принципа на управление в Toyota
В основата на резултатите на Toyota и нейната производствена система лежат 14 важни управленски принципа, които оформят фирмената й култура и са предпоставка за създаването на качество и постигане на ефективност.
Четиринадесетте принципа за управление на Toyota са:
- Базирайте управленските си решения на далновидна философия, дори за сметка на краткосрочни финансови цели;
- Създайте непрекъснат поток в процеса, за да извадите проблемите на повърхността;
- Използвайте изтеглящи системи за избягване на свръхпроизводството;
- Изравнете работното натоварване (хейджунка);
- Изградете култура за спиране и решаване на проблемите, за да постигнете необходимото качество отведнъж;
- Стандартизираните задачи са основата за непрекъснато усъвършенстване и делегиране права на работниците;
- Използвайте визуални контролни средства, за да не останат никакви скрити проблеми;
- Използвайте само надеждна, напълно изпитана технология, която служи на хората ви и на процесите;
- Създайте ръководители, които разбират задълбочено работата, вдъхват живот на философията и я преподават и на другите;
- Създайте изключителни хора и екипи, които следват философията на вашата компания;
- Отнасяйте се с уважение към широката си мрежа от партньори и доставчици, като ги предизвиквате и им помагате да се усъвършенстват;
- Идете и вижте сами, за да разберете изцяло ситуацията (генчи генбуцу);
- Вземайте решенията бавно чрез консенсус, внимателно преценявайки всички възможности; изпълнявайте ги бързо (немаваши);
- Превърнете се в самообучаваща се организация чрез безжалостна критика (хансей) и непрестанно усъвършенстване (кайзен).
Четиринадесетте принципа на управление на Toyota са базирани на ясна логика и много емпирични наблюдения.
Научи повече в статията “14 принципа на управление в Toyota”.
TPS и работа в екип
По-горе се спомена, че един от управленските инструменти, присъщи за производствената система на Toyota, е работата в екип.
По този повод, в своята книга “Пътят на Toyota”, известният изследовател на TPS Джефри Лайкър отбелява следното:
“Заговорите ли някого в Toyota за производствената система, едва ли ще можете да избегнете лекция за значението на работата в екип. Производствената система помага на екипите да извършват работа с добавена стойност.”
Важността на работата в екип е въплатена в единадесетия принцип на Toyota – “Създайте изключителни хора и екипи, които следват философията на вашата компания”. Това не е случайно.
Философията и ценностите на Toyota се основават на разбирането, че хората са изключително ценен ресурс. Мениджърите в компанията разбират, че е критично важно да се управлява човешката мотивация, както и способността на компанията да създават лидери, екипи, култура.
Какво е специфичното в екипите и организационната среда на Toyota?
В един типичен завод обикновено различни мениджъри отговарят за качеството, за производителността на труда, за поддръжката на оборудването, за намаляването на времето за производство на продукта.
В Toyota за всичко това, което на практика е производствената им система, отговарят не мениджърите, а екипите в производствените цехове. Нещо повече, тези екипи са поставени на върха в йеархията на компанията.
Причина за това управленско решение е една културна ценност в Toyota, а именно добавената стойност за клиента. Екипите в Toyota са овластени да създават тази добавена стойност за клиента.
Ако направим сравнение със стандартите на различни компании или пък с принципите на Питър Дракър – всепризнат гуру на мениджънта – на пръв поглед бихме казали, че Toyota е компания с неефективна организационна структура. Преди всичко ще ни се стори, че в нея съществува разточителна норма на управляемост.
Например, ръководителите на екипи в Toyota управляват малко на брой работници – от 4 до 8 души, което е неособено голям обхват на контрол. Следващото равнище в йеархията са груповите ръководители на екипи, които управлвяват 3 или 4 екипа.
Работата на участниците в екипите в Toyota е силно стандартизирана. Тя се състои задължително от три елемента:
- “Тактово време – времето, необходимо за изпълнение за определена работа;
- Последователност на работата;
- Количество запаси, за да се извърши всяка една работа.
Всеки екип в Toyota има постоянна задача да разрешава проблема с подобряване на трите елемента на стандарта.
Струва си да се направи едно бързо сравнение на тази практика с препоръките на бащата на научното управление Фредерик Тейлър.
В началото на XX век Тейлър преппръчва на компаниите, че правилното е мениджърите да разработват ясни стандарти и да обучават работниците как да се справят с тях, след което да се възнаграждават подобаващо онези работници, които надхвърлят изискванията за количество продукция, тъй като това ще създава мотивация в работниците да бъдат още по-производителни. Този тип на управленско мислене доминира дълги години в компаниите от Западния свят.
За сравнение, виждаме как в Toyota екипите са овластени да извършват на практика типична мениджърска работа. По-конкретно, екипите в Toyota са тези, които непрекъснато мислят, предлагат и разработват подобрения в стандартите за работа.
Така например, през 2003 г. само в един от заводите на Toyota в САЩ, са постъпили около 80 000 предложения за подобрения на работните процеси, които са отправени само от екипите в монтажния цех. От тях заводът внедрява 99 %.
В същото време, мениджърите на екипи в Toyota също имат какво да правят. Те извършват рутинни проверки за качество, осигуряват спазването на стандартите, съдействат (подпомагат) работата на екипа да подобрява и усъвършенства стандартите и процесите, осигуряват части (запаси), за да може екипът да изпълнява стандарта за време, заместват работници, които отсъстват от работа и др.
Груповите ръководители на екипи, от своя страна, планират месечното производство, графиците за работа и отпуски, анализират резултатите от рутинните проверки на качеството, участват в проектни екипи за усъвършенстване на производствения процес и намаляване на разходите, грижат се за безопасните условия на работа, кооридинират извършването на основни ремонти, подпомагат развитието на екипите в професионално отношение.
Очевидно е, че работата на екипите, мениджърите на екипи и груповите ръководители в Toyota е интересна и сама по себе си мотивира. Работниците в Toyota не се разглеждат като роботи, които следва да бъдат направени да действат още по ефективно, както счита навремето Тейлър, че трябва да се прави.
Чрез екипната атмосфера в Toyota, служителите удовлетворяват своите потребности от принадлежност и обвързване с хора, които като тях изповядват сходни фирмени ценности, стил на работа и начин на живот. Освен това, екипите в Toyota са овластени да експериментират, внедряват и оценяват постиженията си, което зарежда служителите със самоувереност и самочувствие, че се развиват и усъвършенстват като личности.
В Toyota са установили, че в резултат на по-големите отговорности, служителите в екипите удовлетворяват още и потребностите си от растеж и признание, което ги мотивира да работят все по-добре.
В тази връзка, във фирмата силно се поощрява “поведението на място” – поведение, което е ориентирано към бързо подобряване на процесите в производствената система.
За целта, ръководителите на Toyota са насърчавани постоянно да са в цеховете и на място, бързо и ефективно, да подпомагат работниците, който откриват проблеми и се опитват да ги разрешат.
В резюме
Производствената система на Toyota възниква в резултат на опитите на висшите мениджъри на Toyota да се адаптира системата за масово производство на Хенри Форд към икономическите реалности в Япония след Втората световна война. С други думи, чуждият опит не се пренася сляпо в Toyota, а се прилага внимателно, според конкретните реалности.
Формирането на производствената система на Toyota красноречиво показва целеустремеността на членовете на фамилията Тойода и техните ключови сътрудници да предвиждат бъдещото развитие на събитията.
С течение на десетилетия, тези висши ръководители на Toyota дават своя личен принос в развитието на производствената идеология на компанията. Приносите се надграждат, подобряват и обогатяват през годините, което всъщност е и едно от най-ценните неща в управлението на една организация.
Успехът на производствената система на Toyota допринася за превръщането на Япония в един от световните лидери в автомобилостроенето и способства за повишаване на производителността на труда в други страни по света.
Прочети повече: Кратка история на мениджмънта.